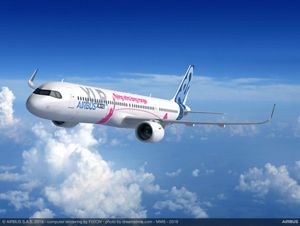
Premium AEROTEC, which was commissioned by Airbus in September 2019 to manufacture the RCT, will complete the structure’s sub-assembly over the next few months at its factory in Augsburg, Germany. This phase involves production of the other RCT parts, followed by structural assembly, systems equipping and testing prior to delivery to Airbus’ major component assembly (MCA) facility in Hamburg early next year, where the tank will be integrated into the aircraft’s rear fuselage.
In addition to the dedicated RCT, other key changes for the A321XLR include a modified landing gear for an increased maximum take-off weight (MTOW) of 101 metric tonnes, uprated brakes, and an optimised wing trailing-edge flap configuration to preserve the same take-off performance and engine thrust requirements as today’s A321neo. By early 2020, the first long-lead components for the initial A321XLR flight-test aircraft were already in production – including the main landing gear forgings by Safran and the first parts for the centre wingbox by Airbus in Nantes.
GOT NEWS? click here
Google News, Bing News, Yahoo News, 200+ publications
The A321XLR, the next evolutionary step in Airbus’ single-aisle family, has been designed to maximise overall commonality with the rest of the A320neo Family, while introducing minimal changes needed to give the aircraft an Xtra Long Range with increased revenue payload and best travel experience with the Airspace cabin. To date, 24 customers have ordered a total of more than 450 A321XLRs, validating the market need for the unique capabilities offered by this aircraft. Flight-testing is due to start in 2022, and service entry from 2023. The A321XLR will provide airlines with a range of up to 4,700nm and a 30% lower fuel burn and CO2 emissions per seat compared with previous-generation competitor aircraft.