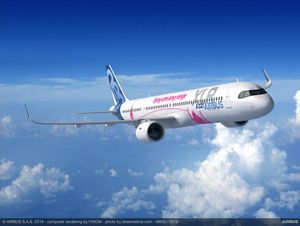
Airbus’ own factory in Hamburg, which will host the Major Component Assembly operations for the rear fuselage equipped with the new rear centre tank, is preparing the necessary jigs and tooling in a new dedicated pilot production line in ‘Hangar 260.’ This operation is deliberately decoupled from the rest of the A320 line, so that starting from next year this pilot line will enable a gradual ramp-up of the A321XLR’s new rear fuselage – to attain maturity without impacting Hamburg’s existing single-aisle production operations.
“The principle of this pilot line in Hamburg means that we can have a ‘stable factory,’” explained O’Donnell. “This will allow us to start ramping-up production of the A321XLR’s aft fuselage Major Component Assembly using longer cycle times to begin with, and with increased level of engineering and support – in particular to ensure the smooth integration of the new rear centre tank and its new fuel systems. Importantly, this new approach will also avoid us putting at risk the rest of single-aisle production. And then, once we’re happy that everything is mature and ‘up-to-speed,’ we can transfer it with confidence into the main production system.”
Regarding the aircraft’s nose and forward fuselage section, parts production is underway at Stelia Aerospace. When these parts are completed, they will be transported to Saint-Nazaire for the nose and forward fuselage Major Component Assembly stage.
GOT NEWS? click here
Google News, Bing News, Yahoo News, 200+ publications
Another key Major Component Assembly structure is the aircraft wing set, for which the UK Broughton team’s particular focus is the A321XLR’s new flap configuration. To this end, the associated tooling trials are in progress for the new ‘movables,’ being performed in conjunction with partners Spirit AeroSystems in Malaysia (inboard flap) and FACC in Austria (outboard flap). The wing’s more conventional fixed components, such as spars and stringers, are taking shape in Broughton and in the associated supply chain. Likewise, production is underway for the landing gear components (Safran, Collins and Triumph); fuel & inerting systems (Collins and Parker Aerospace); and the engine pylons (at Airbus’ dedicated production plant in St. Eloi, Toulouse). ‘Cabin and cargo’ systems are currently in the testing phase to validate the A321XLR’s extra-long-range passenger comfort elements.
Through exceptional international collaboration, the A321XLR is now on its way towards entry into service.